![]() |
Injection molding |
Injection molding digunakan untuk menghasilkan berdinding tipis plastik
untuk berbagai macam aplikasi, salah satu perumahan paling umum plastik
yang. Perumahan plastik adalah kandang berdinding tipis, sering membutuhkan banyak tulang rusuk dan bos pada interior.
Ini perumahan digunakan dalam berbagai produk termasuk peralatan rumah
tangga, elektronik konsumen, alat-alat listrik, dan dashboard seperti
otomotif. Umum lainnya berdinding tipis produk meliputi berbagai jenis wadah terbuka, seperti ember. Injection molding juga digunakan untuk memproduksi beberapa barang sehari-hari seperti sikat gigi atau mainan plastik kecil. Banyak peralatan medis, termasuk katup dan alat suntik, diproduksi menggunakan injection molding juga.
Kembali ke atas Kemampuan
Disclaimer: Semua spesifikasi proses mencerminkan kisaran perkiraan kemampuan proses dan harus dilihat hanya sebagai panduan. Kemampuan yang sebenarnya tergantung pada produsen, peralatan, bahan, dan persyaratan bagian.
Kembali ke atas |
Proses Siklus
Siklus
proses untuk injection molding sangat pendek, biasanya antara 2 detik
dan 2 menit, dan terdiri dari empat tahapan sebagai berikut:
- Clamping - Sebelum injeksi bahan ke dalam cetakan, dua bagian cetakan pertama harus aman ditutup oleh unit klem. Setiap setengah dari cetakan terpasang pada mesin injection molding dan satu setengah diperbolehkan untuk slide. Unit penjepit hidrolik mendorong cetakan bagian bersama-sama dan mengerahkan kekuatan yang cukup untuk menjaga aman cetakan tertutup sementara bahan yang disuntikkan. Waktu yang diperlukan untuk menutup dan klem cetakan tergantung pada mesin - mesin yang lebih besar (orang-orang dengan kekuatan menjepit lebih besar) akan membutuhkan lebih banyak waktu. Kali ini dapat diperkirakan dari waktu siklus mesin kering.
- Injeksi - Bahan baku plastik, biasanya dalam bentuk pelet, dimasukkan ke dalam mesin injection molding, dan maju ke cetakan oleh unit injeksi. Selama proses ini, bahan yang meleleh oleh panas dan tekanan. Plastik cair kemudian disuntikkan ke dalam cetakan sangat cepat dan penumpukan kemasan tekanan dan memegang materi. Jumlah bahan yang disuntikkan disebut sebagai tembakan. Waktu injeksi sulit untuk menghitung secara akurat karena aliran kompleks dan berubah dari plastik cair ke dalam cetakan. Namun, waktu injeksi dapat diperkirakan dengan volume menembak, tekanan injeksi, dan kekuasaan injeksi.
- Pendinginan - Plastik cair yang ada di dalam cetakan mulai dingin segera karena membuat kontak dengan permukaan cetakan interior. Seperti plastik mendingin, itu akan memperkuat ke dalam bentuk bagian yang diinginkan. Namun, selama pendinginan beberapa bagian penyusutan dapat terjadi. Kemasan bahan dalam tahap injeksi memungkinkan material tambahan untuk mengalir ke cetakan dan mengurangi jumlah penyusutan terlihat. Cetakan tidak dapat dibuka sampai waktu pendinginan yang diperlukan telah berlalu. Waktu pendinginan dapat diperkirakan dari sifat termodinamika beberapa plastik dan ketebalan dinding maksimum bagian.
- Ejeksi - Setelah cukup waktu telah berlalu, bagian didinginkan dapat dikeluarkan dari cetakan oleh sistem ejeksi, yang melekat ke bagian belakang cetakan. Ketika cetakan dibuka, mekanisme yang digunakan untuk mendorong bagian dari cetakan. Angkatan harus diterapkan untuk mengeluarkan bagian karena selama pendinginan bagian menyusut dan melekat pada cetakan. Dalam rangka memfasilitasi pengusiran bagian, agen pelepas cetakan dapat disemprotkan ke permukaan rongga cetakan sebelum injeksi material. Waktu yang dibutuhkan untuk membuka cetakan dan mengeluarkan bagian yang dapat diperkirakan dari waktu siklus mesin kering dan harus mencakup waktu untuk bagian yang jatuh bebas dari cetakan. Setelah bagian tersebut dikeluarkan, cetakan bisa menjepit ditutup untuk tembakan berikutnya untuk disuntikkan.
Setelah siklus injection molding, beberapa pengolahan pasca biasanya diperlukan. Selama pendinginan, bahan dalam saluran cetakan akan memperkuat melekat pada bagian. Ini materi berlebih, bersama dengan flash yang telah terjadi, harus dipangkas dari bagian, biasanya dengan menggunakan pemotong.
Untuk beberapa jenis bahan, seperti termoplastik, bahan memo bahwa
hasil dari pemangkasan dapat didaur ulang dengan ditempatkan ke dalam
penggiling plastik, juga disebut regrind mesin atau granulators, yang
regrinds bahan bekas menjadi pelet. Karena beberapa degradasi sifat material, regrind harus dicampur dengan bahan baku dalam rasio regrind yang tepat untuk digunakan kembali dalam proses injection molding.

Injeksi dibentuk bagian
Kembali ke atas
Peralatan
Injeksi mesin cetak memiliki banyak komponen dan tersedia dalam
konfigurasi yang berbeda, termasuk konfigurasi horisontal dan
konfigurasi vertikal.
Namun, terlepas dari desain mereka, mesin injection molding semua
memanfaatkan sumber daya, unit injeksi, perakitan cetakan, dan unit klem
untuk melakukan empat tahap dari siklus proses.
Unit injeksi
Unit injeksi bertanggung jawab untuk kedua pemanasan dan menyuntikkan bahan ke dalam cetakan. Bagian pertama dari unit ini adalah hopper, sebuah wadah besar ke yang baku plastik dituangkan. Hopper memiliki bawah terbuka, yang memungkinkan material untuk memberi makan ke dalam barel. Laras berisi mekanisme untuk pemanasan dan menyuntikkan bahan ke dalam cetakan. Mekanisme ini biasanya injektor domba jantan atau sekrup reciprocating. Sebuah injektor ram kekuatan material ke depan melalui bagian dipanaskan dengan ram atau plunger yang biasanya hidrolik. Saat ini, teknik yang lebih umum adalah penggunaan sekrup reciprocating.
Sebuah sekrup reciprocating bergerak materi maju oleh kedua berputar
dan meluncur secara aksial, yang didukung oleh baik motor hidrolik atau
listrik. Materi yang memasuki alur sekrup dari hopper dan maju ke arah cetakan sebagai sekrup berputar. Meskipun canggih, bahan yang meleleh oleh tekanan, gesekan, dan pemanas tambahan yang mengelilingi sekrup reciprocating.
Plastik cair kemudian disuntikkan ke dalam cetakan sangat cepat melalui
nosel di ujung laras oleh penumpukan tekanan dan tindakan maju sekrup. Hal ini tekanan yang meningkat memungkinkan material yang akan dikemas dan menahan paksa dalam cetakan. Setelah bahan ini telah memperkuat dalam cetakan, sekrup dapat menarik kembali dan isi dengan lebih banyak bahan untuk tembakan berikutnya.
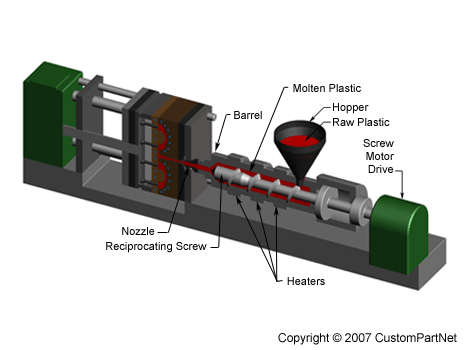
Injection molding mesin - Unit Injeksi
Clamping Unit
Sebelum injeksi plastik cair ke dalam cetakan, dua bagian cetakan pertama harus aman ditutup oleh unit klem.
Ketika cetakan terpasang pada mesin injection molding, masing-masing
setengah adalah tetap ke piring besar, yang disebut sebuah pelat.
Setengah bagian depan dari cetakan, disebut rongga cetakan, dipasang ke
pelat stasioner dan sejalan dengan nosel dari unit injeksi. Setengah belakang cetakan, yang disebut inti cetakan, dipasang ke pelat bergerak, yang slide sepanjang bar dasi.
Motor hidrolik actuates menjepit klem bar yang mendorong pelat bergerak
menuju pelat stasioner dan mengerahkan kekuatan yang cukup untuk
menjaga aman cetakan tertutup sementara bahan yang disuntikkan dan
kemudian mendingin. Setelah waktu pendinginan yang diperlukan, cetakan ini kemudian dibuka oleh motor menjepit.
Sebuah sistem ejeksi, yang melekat ke bagian belakang cetakan, yang
digerakkan oleh ejektor bar dan mendorong bagian dipadatkan keluar dari
rongga terbuka.
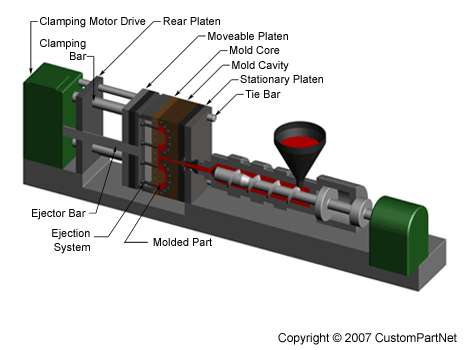
Injection molding mesin - Clamping Unit
Spesifikasi mesin
Injeksi mesin cetak biasanya ditandai dengan tonase dari kekuatan penjepit yang mereka sediakan. Gaya penjepit yang diperlukan ditentukan oleh area proyeksi dari bagian dalam cetakan dan tekanan yang bahan yang disuntikkan. Oleh karena itu, bagian yang lebih besar akan membutuhkan kekuatan penjepit yang lebih besar. Juga, bahan-bahan tertentu yang membutuhkan tekanan injeksi yang tinggi mungkin memerlukan mesin tonase tinggi. Ukuran dari bagian ini juga harus sesuai dengan spesifikasi mesin lain, seperti kapasitas ditembak, penjepit stroke, ketebalan cetakan minimal, dan ukuran pelat.
Injeksi bagian dicetak dapat sangat bervariasi dalam ukuran dan karenanya memerlukan langkah-langkah untuk menutupi rentang yang sangat besar. Akibatnya, mesin cetak injeksi dirancang untuk mengakomodasi setiap rentang kecil dari spektrum yang lebih besar dari nilai-nilai. Spesifikasi sampel ditunjukkan di bawah ini untuk tiga model yang berbeda (Babyplast, Powerline, dan Maxima) dari mesin injection moulding yang diproduksi oleh Cincinnati Milacron.
Injeksi bagian dicetak dapat sangat bervariasi dalam ukuran dan karenanya memerlukan langkah-langkah untuk menutupi rentang yang sangat besar. Akibatnya, mesin cetak injeksi dirancang untuk mengakomodasi setiap rentang kecil dari spektrum yang lebih besar dari nilai-nilai. Spesifikasi sampel ditunjukkan di bawah ini untuk tiga model yang berbeda (Babyplast, Powerline, dan Maxima) dari mesin injection moulding yang diproduksi oleh Cincinnati Milacron.
Babyplast | Powerline | Maxima | |
Clamp kekuatan (ton) | 6.6 | 330 | 4400 |
Ditembak kapasitas (oz.) | 0,13-0,50 | 8-34 | 413 - 1054 |
Clamp stroke (masuk) | 4.33 | 23.6 | 133.8 |
Min. ketebalan cetakan (masuk) | 1.18 | 7.9 | 31.5 |
Pelat ukuran (masuk) | 2,95 x 2,95 | 40,55 x 40,55 | 122,0 x 106,3 |
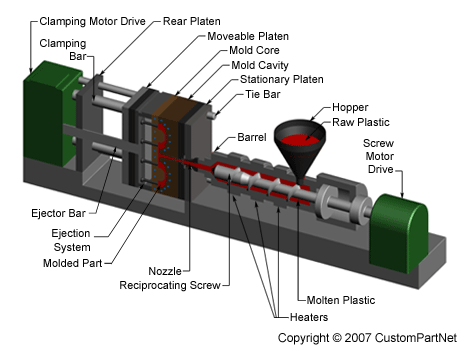
Mesin injection molding
Kembali ke atas
Tooling
Proses injection molding menggunakan cetakan, biasanya terbuat dari baja atau aluminium, sebagai perkakas kustom. Cetakan memiliki banyak komponen, tetapi dapat dibagi menjadi dua bagian.
Setiap setengah terpasang di dalam mesin injection molding dan setengah
belakang diperbolehkan untuk slide sehingga cetakan dapat dibuka dan
ditutup sepanjang garis perpisahan cetakan itu. Dua komponen utama dari cetakan adalah inti cetakan dan rongga cetakan.
Ketika cetakan ditutup, ruang antara inti cetakan dan rongga cetakan
bentuk rongga bagian, yang akan diisi dengan plastik cair untuk membuat
bagian yang diinginkan. Beberapa-rongga cetakan kadang-kadang digunakan, di mana dua bagian cetakan bentuk rongga beberapa bagian yang identik.
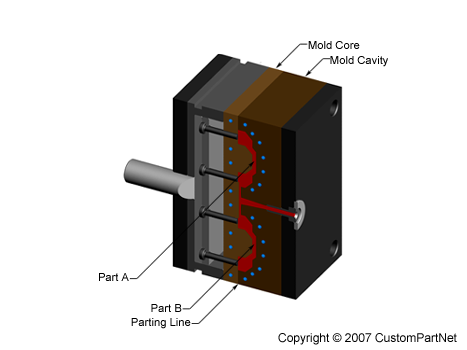
Mold ikhtisar
Cetakan dasar
Inti cetakan dan rongga cetakan masing-masing dipasang ke dasar cetakan, yang kemudian tetap ke platens dalam mesin injection molding. Setengah bagian depan dari dasar cetakan termasuk piring dukungan, dimana rongga cetakan terpasang, bushing sariawan, di mana bahan akan mengalir dari nosel, dan cincin lokasi, dalam rangka untuk menyelaraskan dasar cetakan dengan nozzle. Setengah bagian belakang dasar cetakan termasuk sistem ejeksi, yang inti cetakan terpasang, dan sepiring dukungan. Ketika unit klem memisahkan bagian cetakan, bar ejektor actuates sistem ejeksi. Bar ejektor mendorong piring ejektor maju dalam kotak ejektor, yang pada gilirannya mendorong pin ejektor ke bagian dicetak. Pin ejektor mendorong bagian dipadatkan keluar dari rongga cetakan terbuka.
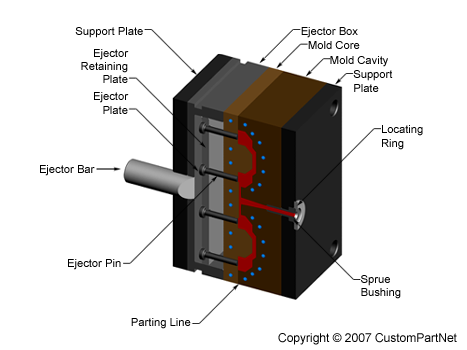
Cetakan dasar
Mold saluran
Agar plastik cair mengalir ke dalam rongga cetakan, beberapa saluran diintegrasikan ke dalam desain cetakan. Pertama, memasuki cetakan plastik cair melalui sariawan. Saluran tambahan, yang disebut pelari, membawa plastik cair dari sariawan ke semua rongga yang harus diisi. Pada akhir setiap pelari, plastik cair memasuki rongga melalui sebuah gerbang yang mengarahkan aliran.
Plastik cair yang mengeras di dalam pelari ini melekat ke bagian
tersebut dan harus dipisahkan setelah bagian telah dikeluarkan dari
cetakan.
Namun, sistem kadang-kadang panas pelari digunakan yang secara
independen panas saluran, yang memungkinkan bahan yang terkandung akan
meleleh dan terlepas dari bagian. Tipe lain dari saluran yang dibangun ke dalam cetakan adalah saluran pendinginan. Saluran ini memungkinkan air mengalir melalui dinding cetakan, berdekatan dengan rongga, dan mendinginkan plastik cair.
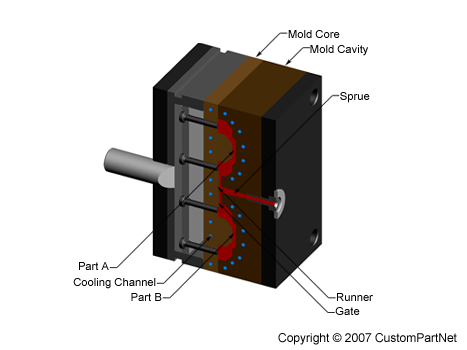
Mold saluran
Desain cetakan
Selain pelari dan gerbang, ada masalah desain banyak lainnya yang harus dipertimbangkan dalam desain cetakan. Pertama, cetakan harus membiarkan plastik cair untuk mengalir dengan mudah ke semua rongga. Sama pentingnya adalah penghilangan bagian dipadatkan dari cetakan, sehingga sudut rancangan harus diterapkan pada dinding cetakan. Desain cetakan juga harus mengakomodasi semua fitur kompleks pada bagian, seperti memotong atau benang, yang akan membutuhkan cetakan potongan tambahan. Sebagian besar perangkat geser ke dalam rongga bagian melalui sisi cetakan, dan karenanya dikenal sebagai slide, atau sisi-tindakan. Jenis yang paling umum dari samping tindakan adalah sisi-inti yang memungkinkan sebuah melemahkan eksternal untuk dibentuk. Perangkat lain masuk melalui akhir cetakan sepanjang arah perpisahan, seperti angkat inti internal, yang dapat membentuk melemahkan internal. Untuk cetakan benang ke bagian tersebut, perangkat unscrewing diperlukan, yang dapat berputar keluar dari cetakan setelah benang telah terbentuk.
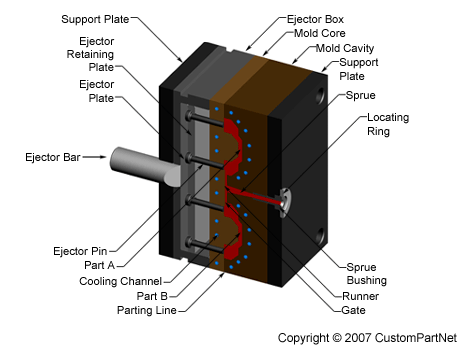
Mold - Tertutup
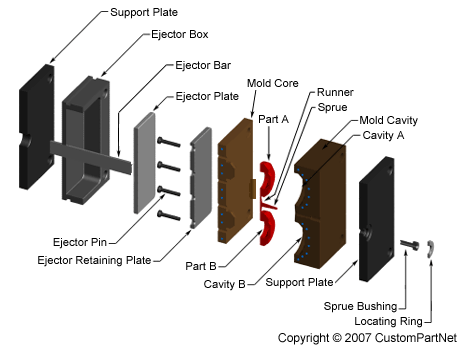
Mold - tampilan Meledak
Kembali ke atas
Bahan
Ada banyak jenis bahan yang dapat digunakan dalam proses injection molding. Kebanyakan polimer dapat digunakan, termasuk semua termoplastik, termoset beberapa, dan beberapa elastomer. Ketika bahan-bahan yang digunakan dalam proses injection molding, bentuk baku mereka biasanya pelet kecil atau serbuk halus. Juga, pewarna dapat ditambahkan dalam proses untuk mengontrol warna dari bagian akhir.
Pemilihan bahan untuk menciptakan bagian injeksi dibentuk tidak
semata-mata didasarkan pada karakteristik yang diinginkan dari bagian
akhir.
Sementara masing-masing bahan memiliki sifat yang berbeda yang akan
mempengaruhi kekuatan dan fungsi bagian akhir, properti ini juga
menentukan parameter yang digunakan dalam pengolahan bahan-bahan.
Masing-masing bahan yang berbeda memerlukan parameter pengolahan dalam
proses injection molding, termasuk temperatur injeksi, tekanan injeksi,
temperatur cetakan, suhu ejeksi, dan waktu siklus. Sebuah perbandingan dari beberapa bahan yang biasa digunakan ditampilkan di bawah ini (Ikuti link untuk mencari bahan pustaka).
Bahan nama | Singkatan | Nama dagang | Deskripsi | Aplikasi |
Asetal | POM | Celcon, Delrin, Hostaform, Lucel | Yang kuat, kaku, kelelahan ketahanan yang sangat baik, ketahanan mulur yang sangat baik, ketahanan kimia, tahan kelembaban, tentu biaya buram putih, rendah / menengah | Bearing, Cams, roda gigi, menangani, komponen pipa, roller, rotor, panduan slide, katup |
Akrilik | PMMA | Diakon, Oroglas, Lucite, Plexiglas | Kaku, rapuh, tahan gores, transparan kejelasan, optik, rendah / menengah biaya | Tampilan berdiri, kenop, lensa, rumah cahaya, panel, reflektor, tanda-tanda, rak, nampan |
Styrene Butadiene akrilonitril | ABS | Cycolac, Magnum, Novodur, Terluran | Kuat, fleksibel, penyusutan cetakan rendah (toleransi ketat), ketahanan kimia, kemampuan elektroplating, alami buram, rendah / biaya menengah | Otomotif (konsol, panel, trim, ventilasi), kotak, pengukur, perumahan, inhalors, mainan |
Selulosa Asetat | CA | Dexel, Cellidor, Setilithe | Tangguh, transparan biaya, tinggi | Menangani, bingkai kacamata |
Poliamida 6 (Nylon) | PA6 | Akulon, Ultramid, Grilon | Kekuatan tinggi, ketahanan lelah, ketahanan kimia, creep rendah, gesekan rendah, hampir buram / putih, menengah / biaya tinggi | Bantalan, ring, roda gigi, roller, roda |
Poliamida 6 / 6 (Nylon) | PA6 / 6 | Popular, Zytel, Radilon | Kekuatan tinggi, ketahanan lelah, ketahanan kimia, creep rendah, gesekan rendah, hampir buram / putih, menengah / biaya tinggi | Menangani, tuas, rumah kecil, ikatan zip |
Poliamida 11 +12 (Nylon) | PA11 +12 | Rilsan, Grilamid | Kekuatan tinggi, ketahanan lelah, ketahanan kimia, creep rendah, gesekan rendah, hampir buram untuk menghapus, biaya yang sangat tinggi | Air filter, frame kacamata, masker keselamatan |
Polycarbonate | PC | Calibre, Lexan, Makrolon | Sangat tangguh perlawanan, suhu, stabilitas dimensi, transparan, biaya tinggi | Otomotif (panel, lensa, konsol), botol, helm pengaman kontainer, rumah, meliputi lampu, reflektor, dan perisai |
Polyester - Termoplastik | PBT, PET | Celanex, Crastin, Lupox, Rynite, Valox | Kaku perlawanan, panas, ketahanan kimia, menengah / biaya tinggi | Otomotif (filter, menangani, pompa), bantalan, Cams, komponen listrik (konektor, sensor), roda gigi, rumah, roller, switch, katup |
Polieter Sulphone | PES | Victrex, Udel | Tangguh, sangat tinggi ketahanan kimia, jelas, biaya yang sangat tinggi | Katup |
Polyetheretherketone | PEEKEEK | Kuat stabilitas, termal, ketahanan kimia, ketahanan abrasi, penyerapan kelembaban rendah | Pesawat komponen, konektor listrik, impeler pompa, segel | |
Polyetherimide | PEI | Ultem | Tahan panas, tahan api, transparan (kekuning-kuningan) | Listrik komponen (konektor, papan, switch), meliputi, sheilds, alat-alat bedah |
Polyethylene - Low Density | LDPE | Alkathene, Escorene, Novex | Ringan, tangguh dan fleksibel, ketahanan kimia yang sangat baik, penampilan lilin alami, biaya rendah | Dapur, rumah, selimut, dan kontainer |
Polyethylene - High Density | HDPE | Eraclene, Hostalen, Stamylan | Tangguh dan kaku, ketahanan kimia yang sangat baik, penampilan lilin alami, biaya rendah | Kursi kursi, rumah, selimut, dan kontainer |
Oksida polyphenylene | PPO | Noryl, Thermocomp, Vamporan | Tangguh tahan, panas, tahan api, stabilitas dimensi, penyerapan air yang rendah, kemampuan elektroplating, biaya tinggi | Otomotif (perumahan, panel), komponen listrik, perumahan, komponen pipa |
Sulfida polyphenylene | PPS | Ryton, Fortron | Sangat kekuatan tinggi, tahan panas, coklat, biaya yang sangat tinggi | Bearing, mencakup, komponen sistem bahan bakar, panduan, switch, dan perisai |
Polipropilena | PP | Novolen, Appryl, Escorene | Ringan, tahan panas, ketahanan kimia yang tinggi, tahan gores, penampilan lilin alami, tangguh dan kaku, biaya rendah. | Otomotif (bumper, selimut, trim), botol, topi, peti kayu, menangani, rumah |
Polistirena - Tujuan Umum | GPPS | Lacqrene, Styron, Solarene | Rapuh, transparan biaya rendah, | Kosmetik kemasan, pena |
Polistirena - dampak Tinggi | PINGGUL | Polystyrol, Kostil, Polystar | Dampak kekuatan, kekakuan, ketangguhan, stabilitas dimensi, secara alami tembus, biaya rendah | Elektronik perumahan, wadah makanan, mainan |
Polivinil Klorida - Plasticised | PVC | Welvic, Varlan | Tangguh, fleksibel, tahan api, transparan atau buram, biaya rendah | Isolasi listrik, peralatan rumah tangga, tabung medis, sol sepatu, mainan |
Polivinil Klorida - Kaku | UPVC | Polycol, Trosiplast | Tangguh, fleksibel, tahan api, transparan atau buram, biaya rendah | Terbuka aplikasi (saluran air, fitting, talang) |
Styrene Acrylonitrile | SAN | Luran, Arpylene, Starex | Kaku, rapuh perlawanan, kimia, tahan panas, biaya hydrolytically stabil, transparan, rendah | Housewares, kenop, jarum suntik |
Termoplastik Elastomer / Karet | TPE / R | Hytrel, Santoprene, Sarlink | Tangguh, fleksibel biaya, tinggi | Ring, komponen listrik, segel, mesin cuci |
Kembali ke atas
Kemungkinan Cacat
Cacat | Penyebab |
Flash |
|
Warping |
|
Bubbles |
|
Terisi bagian |
|
Sink tanda |
|
Ejektor tanda |
|
Banyak cacat di atas disebabkan oleh laju pendinginan non-seragam.
Sebuah variasi dalam tingkat pendinginan dapat disebabkan oleh
non-seragam ketebalan dinding atau non-seragam temperatur cetakan.
Kembali ke atas
Aturan desain
Maksimum ketebalan dinding
- Penurunan ketebalan dinding maksimum bagian untuk mempersingkat waktu siklus (injeksi waktu dan pendinginan waktu khusus) dan mengurangi volume bagian
- Seragam ketebalan dinding akan memastikan pendinginan yang seragam dan mengurangi cacat
Corners
- Sudut putaran untuk mengurangi konsentrasi stres dan patah
- Jari-jari dalam harus setidaknya ketebalan dinding
Draf
- Terapkan sudut draft 1 ° - 2 ° untuk semua dinding sejajar dengan arah perpisahan untuk memfasilitasi menghapus bagian dari cetakan.
Iga
- Tambahkan rusuk untuk dukungan struktural, daripada meningkatkan ketebalan dinding
- Orient rusuk tegak lurus dengan sumbu lentur tentang yang mungkin terjadi
- Ketebalan tulang rusuk harus 50-60% dari dinding untuk yang mereka dilampirkan
- Tinggi tulang rusuk harus kurang dari tiga kali ketebalan dinding
- Putaran sudut pada titik lampiran
- Terapkan sudut draft setidaknya 0,25 °
Atasan
- Ketebalan dinding bos sebaiknya tidak lebih dari 60% dari ketebalan dinding utama
- Jari-jari di pangkalan harus minimal 25% dari ketebalan dinding utama
- Harus didukung oleh tulang rusuk yang terhubung ke dinding yang berdekatan atau dengan gussets di pangkalan.
- Jika atasan harus ditempatkan di dekat sudut, itu harus diisolasi dengan menggunakan tulang rusuk.
Memotong
- Minimalkan jumlah memotong eksternal
- Memotong eksternal membutuhkan sisi-core yang menambah biaya perkakas
- Beberapa memotong eksternal sederhana dapat dibentuk dengan memindahkan garis perpisahan
![]() Sederhana eksternal melemahkan | ![]() Cetakan tidak dapat memisahkan | ![]() Garis perpisahan baru memungkinkan melemahkan |
- Mendesain ulang fitur dapat menghapus melemahkan eksternal
- Minimalkan jumlah memotong internal yang
- Memotong internal sering membutuhkan angkat inti internal yang menambah biaya perkakas
- Merancang sebuah lubang di sisi bagian dapat memungkinkan sisi-inti untuk membentuk sebuah melemahkan internal yang
- Mendesain ulang bagian dapat menghapus melemahkan internal yang
- Minimalkan jumlah aksi arah samping
- Tambahan samping aksi arah akan membatasi jumlah rongga mungkin dalam cetakan
Thread
- Jika mungkin, fitur dengan benang eksternal harus berorientasi tegak lurus terhadap arah perpisahan.
- Fitur threaded yang sejajar dengan arah perpisahan akan memerlukan perangkat unscrewing, yang sangat menambah biaya perkakas.
Kembali ke atas
Biaya Driver
Biaya bahan
Biaya produksi
Tooling biaya
Biaya bahan ditentukan oleh berat bahan yang diperlukan dan harga satuan bahan yang. Berat bahan jelas merupakan hasil dari volume bagian dan kepadatan materi, namun, ketebalan dinding maksimum bagian juga dapat berperan. Berat bahan yang diperlukan termasuk materi yang mengisi saluran cetakan. Ukuran saluran-saluran, dan karenanya jumlah bahan, sangat ditentukan oleh ketebalan bagian.
Biaya produksi
Biaya produksi terutama dihitung dari tarif per jam dan waktu siklus.
Tingkat jam sebanding dengan ukuran mesin injection molding yang
digunakan, sehingga sangat penting untuk memahami bagaimana mempengaruhi
pemilihan desain bagian mesin. Injeksi mesin cetak biasanya disebut dengan tonase dari gaya penjepitan yang mereka sediakan. Gaya penjepitan yang diperlukan ditentukan oleh area proyeksi bagian dan tekanan yang bahan yang disuntikkan.
Oleh karena itu, bagian yang lebih besar akan membutuhkan kekuatan
penjepit yang lebih besar, dan karenanya mesin yang lebih mahal. Juga, bahan-bahan tertentu yang membutuhkan tekanan injeksi yang tinggi mungkin memerlukan mesin tonase tinggi. Ukuran dari bagian ini juga harus sesuai dengan spesifikasi mesin lain, seperti stroke klem, ukuran pelat, dan kapasitas ditembak.
Waktu siklus bisa dipecah ke dalam waktu injeksi, pendinginan waktu, dan waktu ulang. Dengan mengurangi salah satu kali, biaya produksi akan diturunkan. Waktu injeksi dapat dikurangi dengan mengurangi ketebalan dinding maksimum bagian dan volume bagian. Waktu pendinginan juga menurun untuk dinding ketebalan lebih rendah, karena mereka membutuhkan waktu lebih sedikit untuk mendinginkan semua jalan melalui. Beberapa sifat termodinamika materi juga mempengaruhi waktu pendinginan. Terakhir, waktu reset tergantung pada ukuran mesin dan ukuran bagian. Sebuah bagian yang lebih besar akan memerlukan gerakan yang lebih besar dari mesin untuk membuka, menutup, dan mengeluarkan bagian, dan mesin yang lebih besar membutuhkan lebih banyak waktu untuk melakukan operasi ini.
Waktu siklus bisa dipecah ke dalam waktu injeksi, pendinginan waktu, dan waktu ulang. Dengan mengurangi salah satu kali, biaya produksi akan diturunkan. Waktu injeksi dapat dikurangi dengan mengurangi ketebalan dinding maksimum bagian dan volume bagian. Waktu pendinginan juga menurun untuk dinding ketebalan lebih rendah, karena mereka membutuhkan waktu lebih sedikit untuk mendinginkan semua jalan melalui. Beberapa sifat termodinamika materi juga mempengaruhi waktu pendinginan. Terakhir, waktu reset tergantung pada ukuran mesin dan ukuran bagian. Sebuah bagian yang lebih besar akan memerlukan gerakan yang lebih besar dari mesin untuk membuka, menutup, dan mengeluarkan bagian, dan mesin yang lebih besar membutuhkan lebih banyak waktu untuk melakukan operasi ini.
Tooling biaya
Biaya perkakas memiliki dua komponen utama - dasar cetakan dan mesin dari rongga. Biaya dasar cetakan terutama dikendalikan oleh ukuran amplop bagian itu. Sebuah bagian yang lebih besar memerlukan dasar, cetakan yang lebih besar, lebih mahal. Biaya mesin rongga dipengaruhi oleh hampir setiap aspek geometri bagian itu.
Sopir biaya utama adalah ukuran rongga yang harus mesin, diukur oleh
area proyeksi rongga (sama dengan luas proyeksi dari bagian dan lubang diproyeksikan) dan kedalamannya. Setiap elemen lain yang akan membutuhkan waktu mesin tambahan akan menambah biaya, termasuk jumlah fitur, permukaan perpisahan, sisi-core, angkat, perangkat unscrewing, toleransi, dan kekasaran permukaan.
Jumlah bagian juga dampak biaya perkakas. Sebuah jumlah produksi yang lebih besar akan membutuhkan cetakan kelas yang lebih tinggi yang tidak akan memakai dengan cepat. Hasil cetakan bahan yang lebih kuat dengan biaya dasar cetakan lebih tinggi dan waktu mesin lagi.
Salah satu pertimbangan terakhir adalah jumlah sisi-aksi arah, yang secara tidak langsung dapat mempengaruhi biaya. Biaya tambahan untuk sisi-core ditentukan oleh berapa banyak yang digunakan. Namun, sejumlah arah dapat membatasi jumlah rongga yang dapat dimasukkan dalam cetakan. Sebagai contoh, cetakan untuk bagian yang membutuhkan 3 sisi-aksi arah hanya dapat berisi 2 rongga. Tidak ada biaya langsung ditambahkan, tapi mungkin bahwa penggunaan rongga lagi yang bisa memberikan penghematan lebih lanjut.
Jumlah bagian juga dampak biaya perkakas. Sebuah jumlah produksi yang lebih besar akan membutuhkan cetakan kelas yang lebih tinggi yang tidak akan memakai dengan cepat. Hasil cetakan bahan yang lebih kuat dengan biaya dasar cetakan lebih tinggi dan waktu mesin lagi.
Salah satu pertimbangan terakhir adalah jumlah sisi-aksi arah, yang secara tidak langsung dapat mempengaruhi biaya. Biaya tambahan untuk sisi-core ditentukan oleh berapa banyak yang digunakan. Namun, sejumlah arah dapat membatasi jumlah rongga yang dapat dimasukkan dalam cetakan. Sebagai contoh, cetakan untuk bagian yang membutuhkan 3 sisi-aksi arah hanya dapat berisi 2 rongga. Tidak ada biaya langsung ditambahkan, tapi mungkin bahwa penggunaan rongga lagi yang bisa memberikan penghematan lebih lanjut.